Cushion Curve
The fundamental objectives of transport packaging materials are to preserve and protect a product from damage through the manufacturing process to delivery at its final destination. Choosing the right packaging material requires a balance of many factors, including ease of handling and storage, weight, cushioning characteristics, manufacturing efficiency, ease of identification, customer requirements, cost, and more.
Design and distribution requirements for transport packaging are more demanding today than ten years ago. Two major factors – commercial globalization and e-commerce – contribute to this phenomenon. With these changes, small parcel distribution is becoming more common. This increases the importance of material selection to provide adequate cushioning at the best possible price.
Determining the correct amount of cushioning is critical to ensure both function and cost-effectiveness. There are two types of data needed by packaging engineers to evaluate the performance of packaging material: static and dynamic data. The following information focuses on dynamic cushion testing for expanded polystyrene (EPS) foam and what considerations are needed to make a valuable assessment of its use in a particular packaging application or when being compared to other materials.
For more information about the cushion curve properties of EPS, read the technical bulletin Cushion Curve Properties of Expanded Polystyrene Packaging.
Terminology
Packaged products encounter a variety of hazards during handling and transportation. Humidity, temperature extremes, pressure changes, compression, shock, and vibration are the most important ones. Shock refers to brief but intense forces, such as when a product is dropped, while vibration refers to the less intense vibration refer to the less intense but longer duration forces that occur during transportation. Since much more is known about a product’s response to shock than vibration, cushioning is designed mainly with shock in mind.
Cushion material evaluation consists primarily of shock and vibration inputs designed to determine the dynamic levels transmitted through a given thickness of the cushion material as a function of the loading on the material and the height of the drop. Other cushion characteristics include density, compressive creep, flexibility, dimensional stability, and anti-static treatment, among others.
Test Protocols
Dynamic cushioning test results are applicable to the EPS foam properties and are not representative of the specific cushioning abilities that would be achieved in a packaging prototype. The procedure used for conducting a cushion curve has a significant influence on the data generated as well as the intended end use of that data.
ASTM D-1596, “Standard Test Method for Dynamic Shock Cushioning Characteristics of Packaging Material” is the most comprehensive and commonly used test method for determining shock attenuation properties of materials. It provides comparative cushion data for packaging materials rather than data for a specific package design. It’s important to note that ASTM D-1596 specifies a method of reporting data but offers no suggestions for interpreting it. A common method of interpreting data is U.S. Military Specification MIL-C-26861. This specification defines materials into classes and grades according to cushioning performances.
Another generic test protocol material against the typical distribution used is D4139. It gauges packaging environments against typical distribution environments.
ISTA 3C, “Package-Products for Parcel Delivery System Shipment 150 lb or Less”, is a general simulation test for individual packaging systems; the package and product are considered together, not separately. It can be used to evaluate the protective performance of a material related to vibration, shock, and other transit stresses. Some conditions, such as moisture, pressure, or unusual handling, may not be covered by this test.
In 1995, the National Motor Freight Committee (NMFC) approved Rule 180, which allows new package designs to be used in transit immediately following the successful completion of specified performance tests. This rule allows new packaging designs to be put into service more quickly and allows shippers to develop packages specifically tailored to the needs of their products.
Performance Guidelines
Cushioning properties are determined based on their ability to provide the necessary protection in terms of inputs such as shock (impact) and vibration. The shock resistance of EPS will depend upon the density and thickness of the foam. Cushion curve data for 1.25, 1.5, and 2.0 pcf at various drop heights indicate that EPS foam can absorb impacts efficiently and recover its physical shape quickly, making it ideal for packaging fragile items within a wide range of weights and sizes.
Cushion curves can be used to determine the bearing area (static loading) and the thickness of a cushioning material required for a particular application. Oversizing the bearing area of cushioning material is as ineffective as under-sizing—excessively bearing will not properly “give” during impact and can transmit abrupt shock and excessive impact deceleration to the falling item. Likewise, insufficient cushion thickness may completely compress or bottom-out during impact. EPS effectively absorbs shock forces and resists deformation when compressed to 50-60% of its original thickness.
EPS protective packaging offers a broad range of physical properties to allow packaging designers to meet the many challenges of protection and distribution. These properties, in combination with appropriate engineering design considerations, provide the design flexibility required to create truly cost-effective protective packaging.
[PDF] Cushion Curve Properties of Expanded Polystyrene Packaging
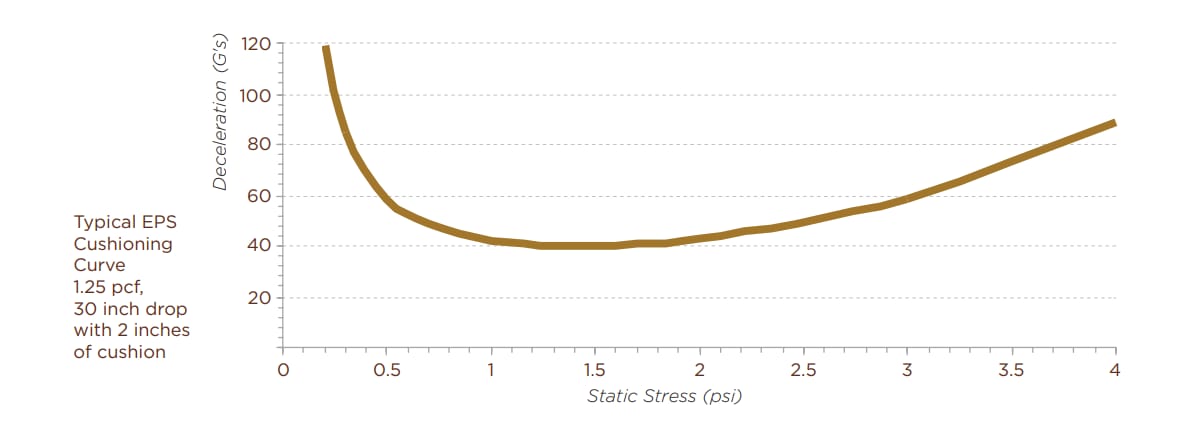
Source: EPS Industry Alliance, 2020, www.epsindustry.org/.